Here are a few fabrics you will see on the website and what makes them special and worth your buy, also a quick tip on how to identify an original from the fake machine-made ones.

Ikat
Fabric: A handwoven fabric whose charm and versatility allows year-round comfort. The technique of making Ikat, known as 'Ikkat' has its origins from around the world, including South East Asia, South America and West Africa. It's an ancient art that was derived from the Malay word, 'Mengikat' which means to tie.
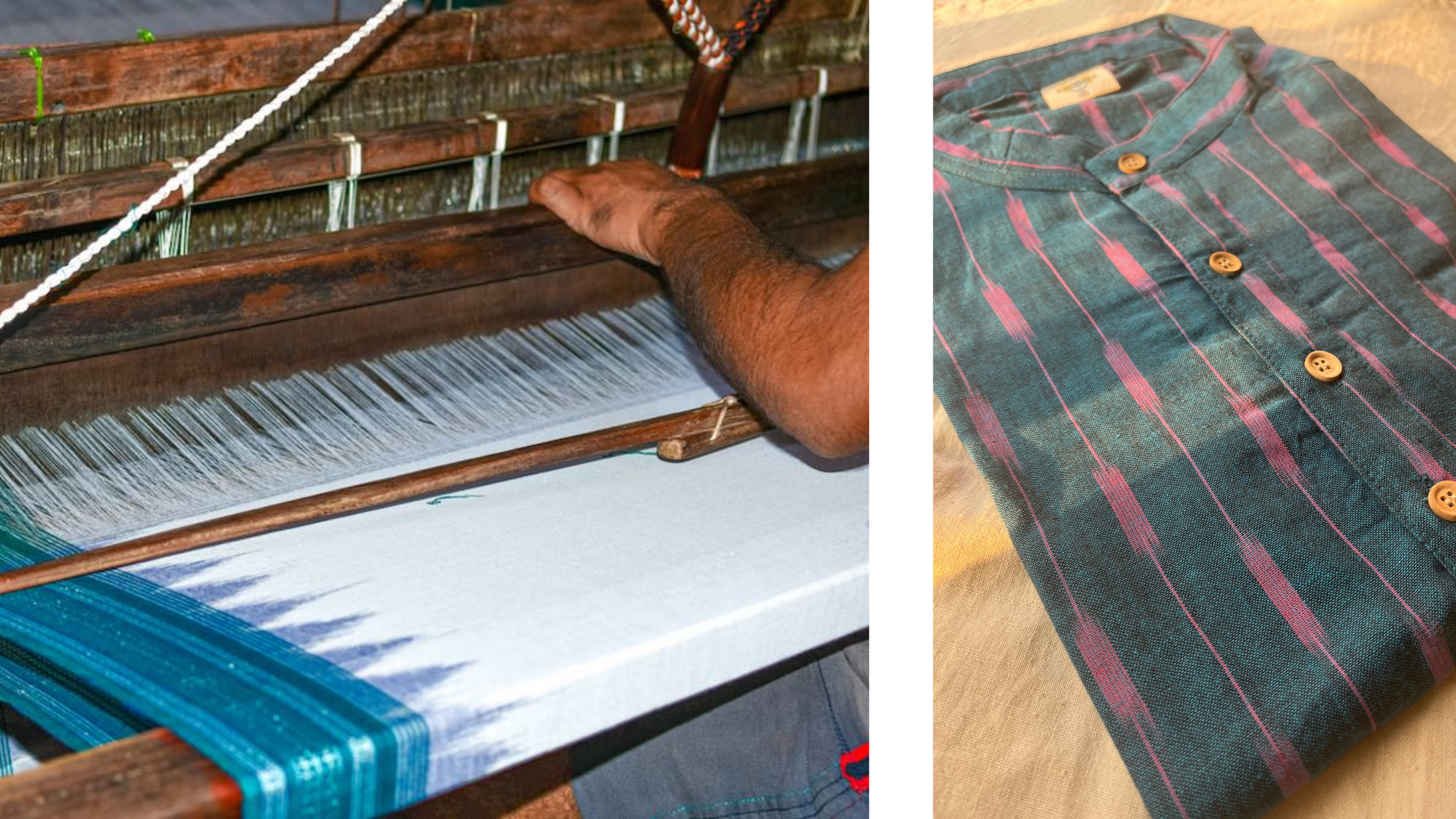
Technique: The technique of producing the Ikat fabric is often called 'Poetry of loom' due to the complexity and beauty of the process. The base fabric used for producing ikat are generally silk & cotton and are dyed by the process of "resist dyeing" where bundles of yarn are tightly wrapped together and dyed as many times as required and to create the desired pattern. Then comes the intricate weaving method that converts the yarns into a beautiful fabric. The designs are made with vertical symmetry which results in a similar pattern on the sides. Such a technique is time-consuming as artisans need to precisely line up the weft yarns for perfect design outcomes.
Identification: An original Ikat fabric will look the same from both sides as the yarn is dyed and then woven. So always check the inner side of the garment.
Hand Block print
Fabric: Hand block printing is a centuries-old art form popular in India, China, and many other East Asian countries, also referred to simply as "block printing" or "woodblock printing". Elaborate designs are created through this technique of hand block printing which includes certain basic components of Buti, Jhal, Bel and Buta constituting smaller patterns in a Block Print.

Technique: The Hand block printing patterns are usually done on textiles like linen, cotton or silk by using wooden blocks. In India, this ancient printing technique utilizes a hand-carved teak wood block that is dipped in dye and stamped by hand onto the fabric. The printing process is the simplest, but the slowest process of textile printing. The result is truly unique as hand block printed fabric connects us to a rich tradition and history of handmade crafts to reach its highest visual expression.
Identification: The Hand block prints used in Adah fabric are yield higher artistic results, some of which are not possible by any other designing method. The way to identify an original hand block print is by looking at irregularities, the fact that it's HAND block printed makes the printing irregular and that's where the beauty lies.
Ajrakh
Fabric: The word 'ajrakh' implies several different notions as it comes from the Arabic word ajrakh, which means blue which is one of the chief colours in ajrakh printing. Others believe the word has been coined from the two Hindi words- aaj rakh, meaning, keep it today as the printing of complex designs is done in parts and goes on for several days.
Technique: Ajrakh is a type of block printing that involves a long and arduous process that requires many stages of printing and washing the fabric repeatedly with different natural dyes and mordants. The technique of resist printing is employed which permits absorption of a dye in the required areas and prohibits absorption on the areas meant not to be coloured. The resist paste is first applied to the fabric then it is dyed manually using wooden hand-carved blocks. This process is repeated several times with different kinds of dyes and blocks to achieve the final design in the desired shade.
Identification: To identify ajrakh one needs to look for fabric with a background of red or blue (though other vegetable dye colours like yellow and green have been introduced) Traditionally four colours were used red (alizarin), blue (indigo), black (iron acetate) white (resist). The ajrakh makers believe that the printed fabric has warm and cool colours which steady the body temperature blue is cooling and red is warm.
Kalamkari
Fabric: Kalamkari refers to the ancient style and is derived from two Hindi words 'Kalam' and 'Kari' which translates into 'pen craft.' It includes a detailed and complicated painting that results in beautiful and elegant designs. flowers, peacock, paisleys and also divine characters from Ramayana and Mahabharata.
Technique: Generally, cotton fabric is used which is first treated with a solution of cow dung and bleach to give a uniform white colour and then dipped in a mixture of buffalo milk and myrobalan to avoid smudging of dyes on the fabric. The fabric is then washed twenty times and sun-dried to make it ready for printing. Kalamkari designs are then painted on the fabric, by hand to fabricate minute detail and it is painted using natural dyes.
At Adah, we have incorporated Machilipatnam style of kalamkari fabric in which the craftsman creates his sketch and its key design features with the help of hand-carved blocks and the gaps are then hand-painted with the bamboo pen.
Identification: Screen and digitally printed ones look perfect whereas authentic hand-painted kalamkari has irregularities and minor stains as they are being hand-painted by artisans. As the fabric is being washed multiple times during the process, they are soft, raw, and earthy.
Handspun Cotton
Fabric: Handspun cotton is artisanal heritage handloom textile, made entirely in hand crafted processes—from spinning the threads on a charkha (spinning wheel) to weaving on handloom. The spinning of cotton is labour intensive and time-consuming.
Technique: Natural fibers of cotton are collected & processed through a series of procedures in order to clean and bundle together. These clean fibers are then spun into yarns manually, which are later used to produce handwoven cotton fabric. On the handloom, the yarns, in the form of warp and weft are woven by the artisan to ultimately produce the handspun cotton. The yarns can also be dyed before weaving to create subtle patterns like checks and stripes.
Identification: The ends of a cotton cloth are usually soft and loose as compared to a machine-woven cloth.
Now that you know more about our fabrics and the intricacy, how about giving them a try and experiencing the comfort yourself? Check out our shop. You are bound to love it!